MPC is method used in automation and system control. MPC assumes the future behavior of the system and use a model of the system to predict its future state. This allows MPC to better respond to changes in input conditions and achieve better control performance. MPC considers constraints of the system. This is useful for controlling systems with physical limitations. MPC can be used for optimizing cost functions such as minimizing energy consumption, maximizing performance, or minimizing control error. In summary, MPC is generally a more powerful and flexible controller than PID, especially for complex systems with constraints.
Despite the excellent properties of MPC, its implementation in industry is not always possible, mainly due to its computational burden. Aim of the project was Random-shooting-based Approximation of Predictive Control and its implemantation on real device and also implementation of reference tracking problem. Despite to MPC, Random shooting is less time consuming and has very simple algorithm. To solve the optimization problem, the random shooting method generates multiple random sequences of control inputs. These sequences are sub-optimal but feasible. For implementation MPC and random-shooting based control we used Flexy device (Figure 1). Flexy represents a simple dynamical system with one actuator (fan) and one sensor (flex resistor). In our experiment we added reference tracking as we can see in Figure 2.
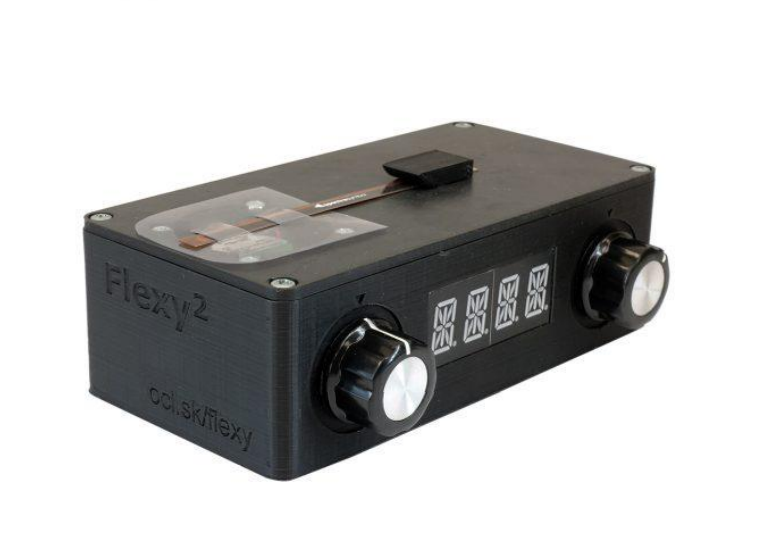
The quality of the best feasible control sequence generated by random shooting algorithm depends on the number Nf which is maximal number of feasible sequences to check. In the first case we set lower value of this parameter and we can see the results in Figure 3. These graphs represent the control performance of the reference tracking for the Flexy device.
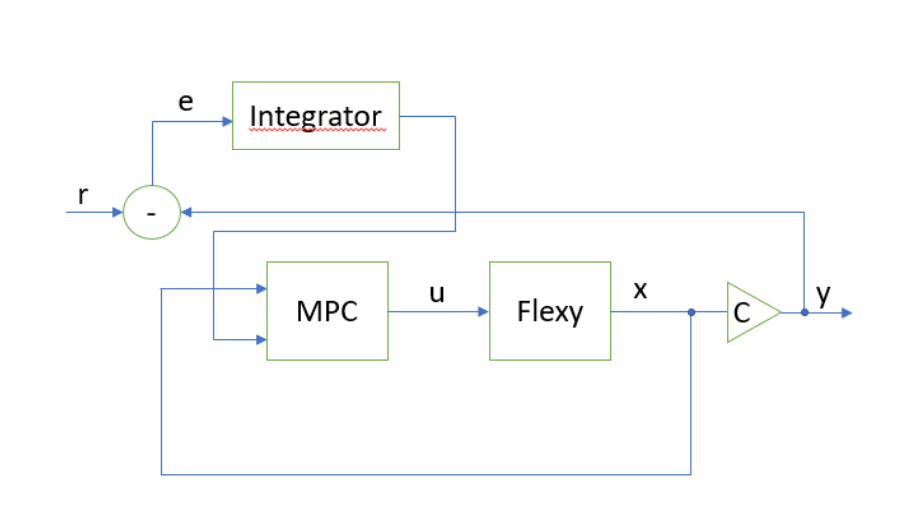
The Table 1, shows the comprasisom between MPC and Random shooting based control. If we set lower Nf, the algorithm is faster but value of cost function is higher in comparison to MPC. In the second case we set higher value of Nf. We can see the results in Figure 4.
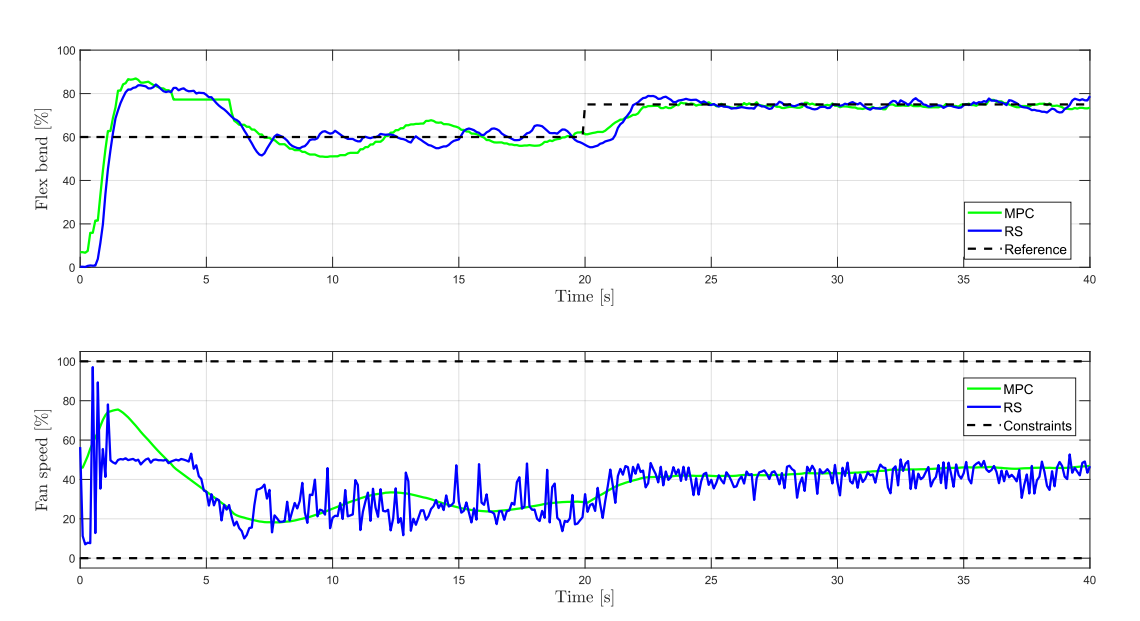
By increasing Nf, cost function is lower, very similar to MPC but the algorithm is slower. From the results we can see a big advantage of random shooting which is the ability to tune computational burden and suboptimality

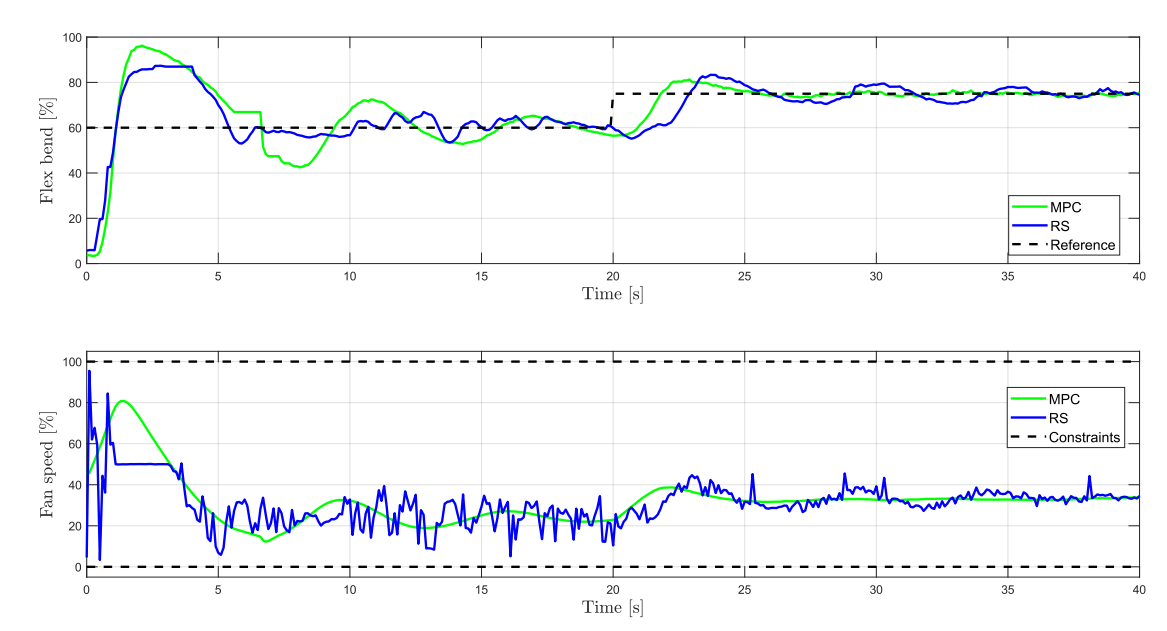
